IP (Ingress Protection) is a measure of an enclosure’s ability to keep out dust and water.
by Allyn Weilacher, Marketing Operations Specialist at Hammond Enclosures
When selecting an enclosure, few things are as important to a customer as its ratings. As the buffer between vital electronic devices and the outside world, an enclosure must meet the demands of the environment around it and manage threats such as dust, water, sunlight, and chemicals.
Quality starts at the design phase, when engineers create a new enclosure with testing guidelines in mind. Submitting completed parts for rigorous independent testing is the ideal way to establish reliable and trustworthy parts in the market.
IP (Ingress Protection) is a measure of an enclosure’s ability to keep out dust and water. IP standards are set by the International Electrotechnical Commission (IEC). The first digit in the IP rating refers to dust protection; the second refers to water protection.
Common dust protection ratings are 5 (dust-protected) and 6 (dust-tight). In the context of IP testing, the relevant water protection digits are 6, 7, and 8. While all three encapsulate a general definition of “watertight,” 6 indicates protection from powerful water jets while 7 and 8 indicate protection after total submersion in water (temporary and continuous, respectively).
The IP testing procedure for enclosures will be discussed later in this article, including a real-world example of the standards Hammond sets for its own IP rated products.
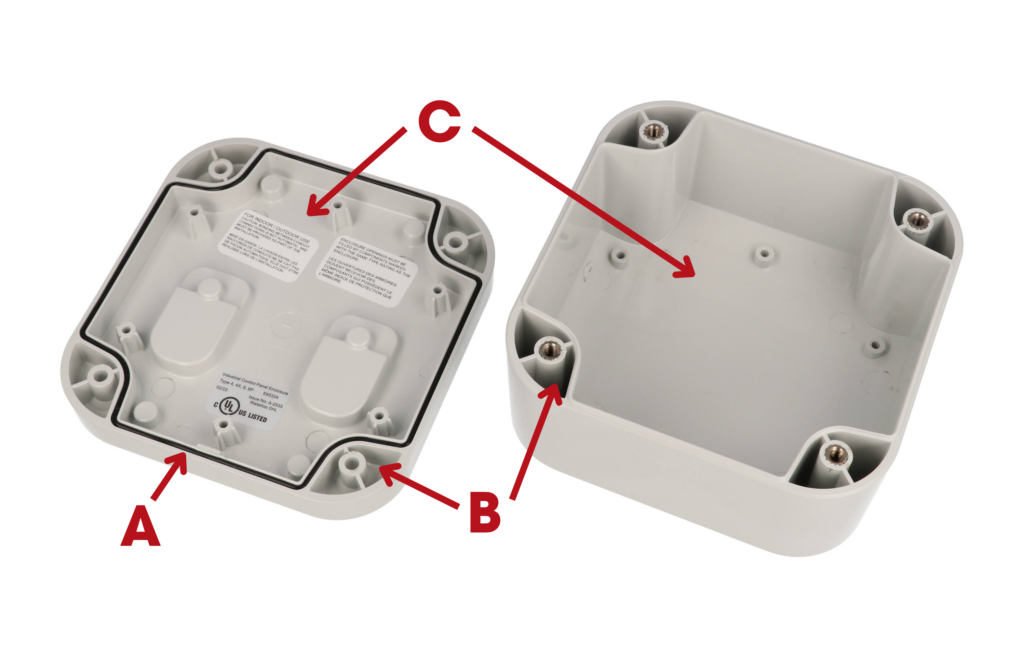
Testing considerations
After contacting an independent testing laboratory and choosing which tests will be performed, the manufacturer sends sample enclosures to the lab. Selecting enclosures for testing is a thoughtful process; while every individual SKU in a series could be tested, the range of samples should at minimum account for any differences in design that might affect ratings, such as size, lid style, or internal features. Manufacturers can use these results to direct product improvement and inform the design of future projects.
The enclosures are pre-assembled with recommended cover screw torque values. Torque is a measure of twisting force and captures both the amount of force applied and distance from the application point. International torque values for enclosure lid screws are given in Newton meters. For example, an enclosure may have a recommended torque range of 30-40 cNm (centi-Newton meters).
Optimal torque ensures not only that the lid is fully seated, but that the gasket is properly situated and compressed to seal the perimeter. Non-porous gaskets, which are typically made from materials like silicone, rubber, and neoprene, are required for a truly watertight seal.
If too little torque is applied, the lid will not seal correctly and liquid can enter the enclosure. If too much torque is applied, there is a risk of damaging the threaded insert, the screw itself, or even the enclosure material, creating structural faults that allow liquid ingress.
Test procedure
Once the lab has received the enclosures, they will begin testing as laid out by IEC 60529:2013 standards. The IP code allows some parameters to be set by the manufacturer.
IPX6: During this test, enclosures are hosed down at a flow rate of 100 liters per minute for 30 seconds per surface (all 6 sides of an enclosure). The nozzle of the hose must comply with certain dimensions to achieve the desired spray pattern for the test. After testing, the enclosure is opened to inspect for water ingress. IP code states that the amount of water in the enclosure “shall not have harmful effects,” and thus some applications may allow a small amount of water. Hammond’s standard is that no water can be inside the enclosure.
IPX7: For this test, the enclosure is submerged in 1 meter of water for 30 minutes. While many labs use a submersion tank with a meter of water, some use a pressure chamber to simulate the same amount of water pressure in a shallower container. Again, the enclosure is opened and cannot have any water ingress inside the gasket area.
IPX8: This test is like the IPX7 procedure but requires submersion in water or equivalent pressure at a length of time specified by the manufacturer, typically 30 or 60 minutes. The IP code states that the submersion depth must exceed the depth used in the IPX7 test, and Hammond’s standard is 2 meters. As before, no water can be inside the gasket area for the enclosure to pass the test.
IP5X, IP6X (Dust-tight): Although many enclosures that pass the IPX6, IPX7, or IPX8 liquid ingress tests are reliably dust-tight as well, separate dust-tight testing can be performed, involving placing the enclosure inside a dust chamber and subjecting it to blown particles. The concentration of dust particles, direction of the gusts, and speed of the fan are all dictated by IEC guidelines.
To qualify for a dust rating of 5 (dust-protected), the enclosure must not accumulate enough dust to affect the normal operation of the enclosure. If no dust is detected inside the enclosure at all, it qualifies for a dust rating of 6 (dust-tight).
Examples
Hammond’s 1557 series is comprised of gasketed plastic enclosures available in both ABS and polycarbonate plastic material.
Similarly to how a water-tight enclosure can reasonably be assumed to be dust-tight, some IP ratings by necessity will cover lower ratings. For example, the IP code states: “Up to and including second characteristic numeral 6, the designation implies compliance also with the requirements for all lower characteristic numerals.”
Therefore, IP66 is automatically compliant for IP61 through IP65. IP67 and IP68, however, do not automatically comply with IP65 and IP66, and this is why Hammond submits polycarbonate enclosures for IP66, IP67, and IP68 testing, even when an IP68 rating is ostensibly the primary goal.
Material properties influence an enclosure’s performance, and ABS plastic versions are submitted for IP66 testing but not IP67 or IP68. These versions use the same mold cavity, gasket, and hardware as the polycarbonate version, but ABS plastic is less rigid than polycarbonate, so the enclosure walls can deform more easily under pressure. Because the pressure is offset to the material, there is also less force keeping the gasket sealed in place. While many ABS enclosures could survive submersion just under the waterline, they will not handle deep water as effectively as polycarbonate enclosures.
Polycarbonate also has the benefit of some natural ultraviolet (UV) resistance, which can be bolstered by UV stabilization treatment of the raw material, making it the plastic material of choice for use outdoors. Gasketed ABS enclosures make sense for use indoors, where the enclosure might still be exposed to some moisture and splashing water.
For a manufacturer, IP certifications provide a key foundation for building consumer trust. When a product has been carefully designed and independently tested, engineers, buyers, compliance specialists, and end users alike will feel empowered to include it on their next BOM.