There are four leading capacitor technologies for automotive power electronics.
by Daniel West, Lead Technical Applications Engineer, Technical Support Group (TSG) at KYOCERA AVX Components
The capacitor symbol on a schematic hides a large amount of information. Automotive power circuitry relies heavily on capacitors for voltage regulation, filtering, decoupling, noise suppression, and overall stability. From electric motors (including EV powertrains) to infotainment ICs, there is a wide range of power requirements and a host of capacitor technologies that would satisfy electrical requirements.
What the schematic symbol hides is that there are many materials that can be used as a dielectric between a set of electrodes to satisfy the requirement of capacitance and voltage in a circuit. However, these materials respond very differently to temperature, vibration, ripple current, frequency, transient voltage, and humidity to name some of the more common parameters that affect capacitor performance.
These parameters vary so much from one capacitor technology to another that there is no single technology that is best for every application. This is where a strong component engineer comes in, but every designer should also know the general benefits and concerns for the dominant capacitor technologies in the automotive industry, which should get them well on their way to a part number for most applications (there are no flux capacitors yet, unfortunately).
The leading capacitor technologies for automotive power electronics are, in no particular order: Ceramic, Tantalum, Aluminum, and Film (plastic film) capacitors.
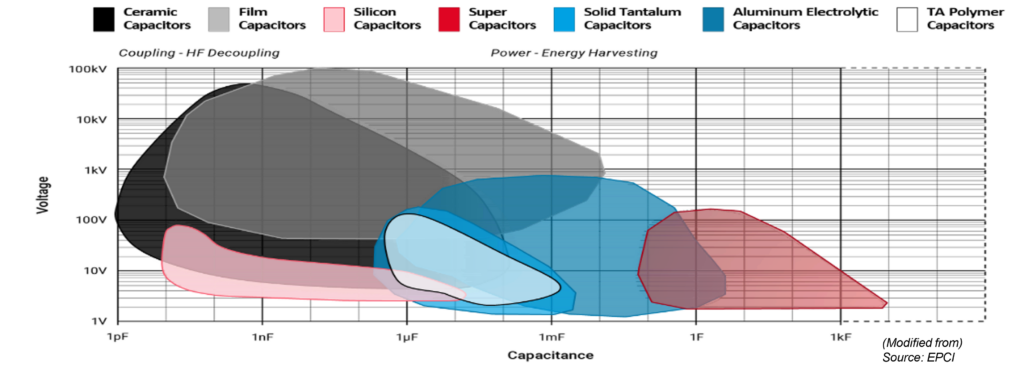
Ceramic Capacitors: These have a combination of very high dielectric constants and small electrode spacing, which afford them relatively high capacitance per volume. They also have the lowest losses, meaning the lowest ESR and ESL potential of the four technologies making them ideal for localized decoupling of high-performance processors.
Their drawbacks arrive in the form of reduced capacitance under applied voltage for high dielectric constant capacitors. NP0/C0G ceramics have low dielectric constants and are virtually immune to diminished capacitance. The capacitance for X7R, X5R, X6S/T, and X8R/L ceramics have reduced capacitance with applied voltage and temperature and gradually lose capacitance over time. The leading suppliers of ceramic capacitors are dedicated to reducing these losses, and it cannot be stressed enough to compare datasheets of capacitors with identical ratings and size. Depending on internal design rules, performance can vary drastically among suppliers.
Tantalum Capacitors: These have the highest capacitance per volume/gram capability. Their volumetric efficiency has been capitalized in SSD hold-up circuits, Mars rovers, and internal defibrillators. These are extremely reliable devices, but they require the most care during design and the raw materials are difficult to source, which makes them more expensive compared to the other capacitors.
These are solid electrolytic devices and have a very thin dielectric thicknesses (angstroms), which enables incredible capacitance density but simultaneously creates an inherent susceptibility to punch through from surge events and low tolerance for reversed polarity. This necessitates strict voltage derating rules, which should be transparent from the supplier; be wary if not.
They also have extremely low capacitance loss with applied voltage and temperature and can be manufactured with a conductive polymer cathode, thereby reducing ESR to a point that it can handle 8x the ripple current of an identical standard MnO2 tantalum capacitor. Leading suppliers include novel moisture resistant materials in the molded epoxy and lead frame that is used to isolate the dielectric from the environment. Tantalums are moisture sensitive prior to mounting and can get up to MSL 3 or 4 depending on design.
Aluminum Electrolytic Capacitors: These are widely used in power supply designs for their massive capacitance and voltage ratings, and their good ripple current performance. They are the most economical capacitor technology. Chief among concerns is reliability. These use a wet electrolyte system that evaporates over time leading to increased ESR causing internal heating, which causes more evaporation, etc. In cold temperatures they have increased ESR due to the wet electrolyte turning solid.
There are ways to increase reliability of course. Sealing technology for the aluminum cans make them more resilient to shock and vibe, and a cathode system can be introduced with an additional layer of polymer mesh that is highly conductive to keep ESR low, yet porous to allow the wet electrolyte to make constant contact with the anode layer to consistently maintain the oxide layer. Hybrid aluminum electrolytic capacitors provide a balanced approach to capacitance and reliability.
Film Capacitors: These are the largest and bulkiest by far among the capacitor technologies. For automotive applications, this seems counterintuitive, but they have attractive features such as self-healing and low loss. If we consider the level of reliability required for EV powertrain circuits, the powertrain ECU and the DC-AC converter would be top notch (hopefully). Film capacitors have a unique feature of having a “soft” failure mode, which simply means reduced capacitance, that is, it does not have a short circuit failure mode.
As a sidenote, there is one other capacitor technology that also fails open circuit, but it doesn’t dominate the automotive power application space: Niobium capacitors can be found in airbag deployment circuits to maintain a small amount of voltage for critical functions. Film capacitors, though, have almost no limit to the capacitance value desired or the voltage rating desired. 100kV ratings and a few dozen millifarad devices are not unheard of.
Film capacitor design is essentially limited by the size and weight constraints involved with shipping the components to the customer. As you may have guessed, overdesigning a film capacitor for an application is quite easy and pays a heavy toll in added weight. Some capacitor designs use oil to disperse heat and reduce corona effects, and these quickly get to tens of kilograms for automotive applications. Leading suppliers optimize weight and performance by using highly advanced thermal and inductive models with decades of material and CAD experience to back up design efforts.
Film capacitor designs are fine tuned to achieve the lowest weight possible while having a very specific lifetime, so volumetric efficiency is limited only by the designer’s knowledge of electrical, thermal, mechanical, and environmental stress that may be applied.
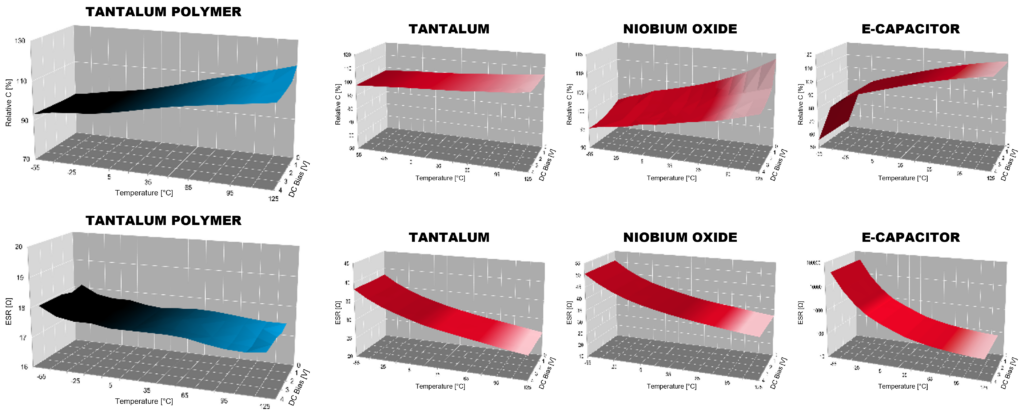
Summary
These general features, benefits, and concerns of the four prominent capacitor technologies hopefully get you to a P/N for the BOM. At least, they will speed discussions with the supplier.
As a recap, ceramics are great for the widest breadth of applications, tantalums for tough designs where capacitance is a must in a small size, aluminums for general purpose filtering with an option for a high reliability hybrid or low ESR polymer, and films are the safest for medium and high power applications (volumetric efficiency is only optimized with advanced models).
www.kyocera-avx.com